Maintenance of the drill bit
Feb 29, 2024
Due to actual drilling conditions, or incorrect operation of the drill bit, wear patterns are often formed.
If it is not judged in advance and re-grinded before its wear cycle arrives, the drill bit will perform poorly or fail prematurely.
Make sure that the drill bit (except alloy teeth) is not in contact with the metal surface
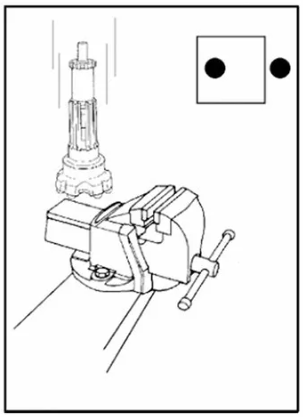
Do not let the bottom of the alloy teeth touch each other
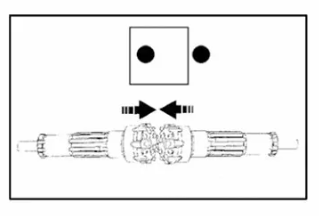
Before any transportation or priority authorization may cause or damage the use, you should remember the number and
serial number of the drill bit to facilitate future inspections.
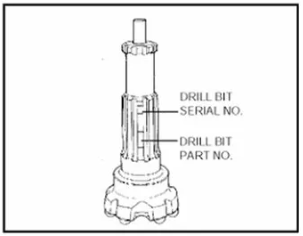
Before assembling the DTH hammer, make sure that all the splines of the drill are coated with grease.
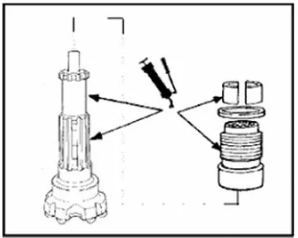
First check whether the plastic tail pipe is installed correctly and whether the exposed height is correct.
The second check is that the plastic tail pipe is not broken, which is usually caused by the linear deviation caused by the
wear of the piston or cylinder. Lack of lubrication can lead to extraction and water corrosion.
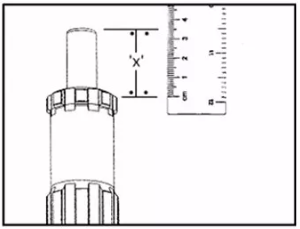
Check for damaged and corroded impact ends. This is usually due to lack of lubrication or the use of mismatched parts
on the piston and impact ends.
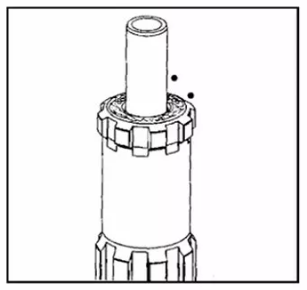
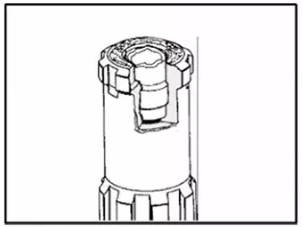
A ruptured impact end is usually caused by severe wear of the piston, circlip, bottom bushing, or retaining ring.
Bottom grinding method-mold grinding
Draw a pencil line along the plane, and then divide the bottom into two symmetrical parts. Lightly grind each part divided
by the pencil line, and do not touch the pencil line. Finally, lightly blend the pencil lines and remove as few alloy teeth as possible.
The purpose of this technology is to remove as few alloy teeth as possible, so that when the grinding is finished, the reground
alloy teeth are spherical and only slightly smaller than the new teeth.
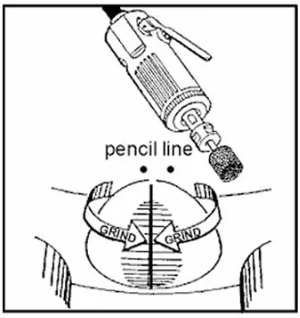
Under the ground conditions of grinding and drilling, not only the alloy teeth will wear, but also the bit body below it.
Excessive wear makes the diameter of the bottom of the drill bit the same as the diameter of the steel body of the drill bit,
which causes the drill bit to jam or tighten in the borehole. Remedy can be done through the following methods.
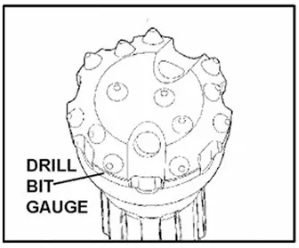
Grind the steel body. Grind the drill head 90 degrees to the bottom of the drill in a circle, and the grinding length is about 4.5 mm.
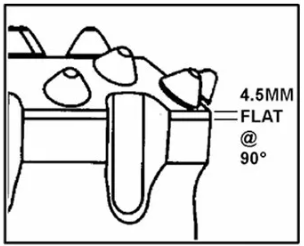
Grind the groove on the bevel. If necessary, grind the chamfered groove in a direction 4 degrees to the axial direction of the drill bit.
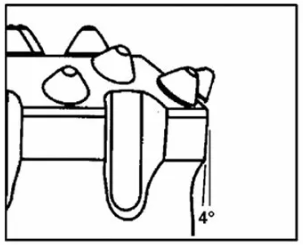
Make sure that the depth of the chip flute is appropriate, and regularly grind it to ensure that the drilled debris can be
discharged smoothly. Make sure that the chip flutes are not deformed, and if necessary, grind them.
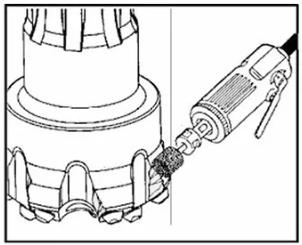
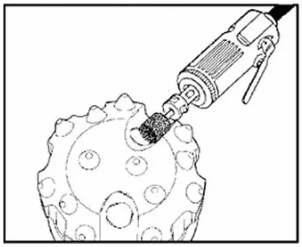
If it is not judged in advance and re-grinded before its wear cycle arrives, the drill bit will perform poorly or fail prematurely.
Make sure that the drill bit (except alloy teeth) is not in contact with the metal surface
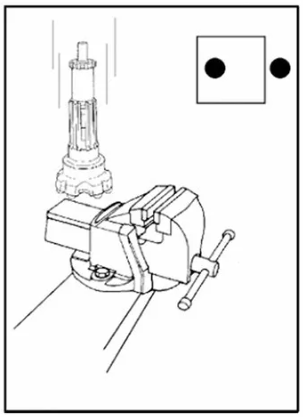
Do not let the bottom of the alloy teeth touch each other
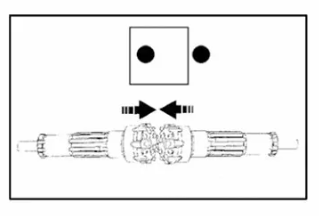
Before any transportation or priority authorization may cause or damage the use, you should remember the number and
serial number of the drill bit to facilitate future inspections.
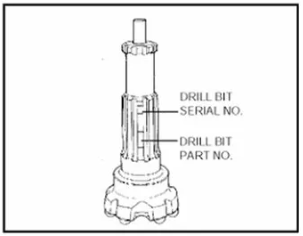
Before assembling the DTH hammer, make sure that all the splines of the drill are coated with grease.
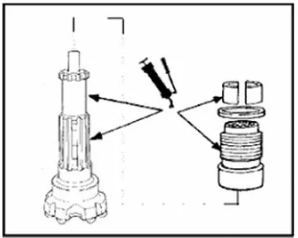
First check whether the plastic tail pipe is installed correctly and whether the exposed height is correct.
The second check is that the plastic tail pipe is not broken, which is usually caused by the linear deviation caused by the
wear of the piston or cylinder. Lack of lubrication can lead to extraction and water corrosion.
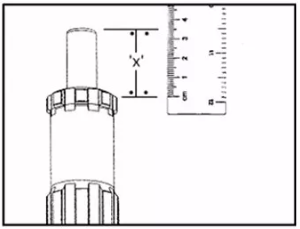
Check for damaged and corroded impact ends. This is usually due to lack of lubrication or the use of mismatched parts
on the piston and impact ends.
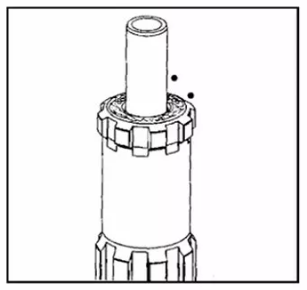
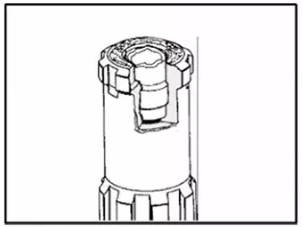
A ruptured impact end is usually caused by severe wear of the piston, circlip, bottom bushing, or retaining ring.
Bottom grinding method-mold grinding
Draw a pencil line along the plane, and then divide the bottom into two symmetrical parts. Lightly grind each part divided
by the pencil line, and do not touch the pencil line. Finally, lightly blend the pencil lines and remove as few alloy teeth as possible.
The purpose of this technology is to remove as few alloy teeth as possible, so that when the grinding is finished, the reground
alloy teeth are spherical and only slightly smaller than the new teeth.
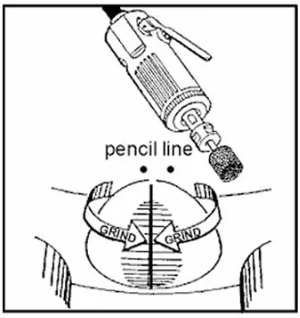
Under the ground conditions of grinding and drilling, not only the alloy teeth will wear, but also the bit body below it.
Excessive wear makes the diameter of the bottom of the drill bit the same as the diameter of the steel body of the drill bit,
which causes the drill bit to jam or tighten in the borehole. Remedy can be done through the following methods.
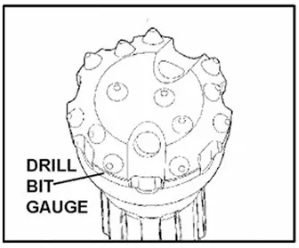
Grind the steel body. Grind the drill head 90 degrees to the bottom of the drill in a circle, and the grinding length is about 4.5 mm.
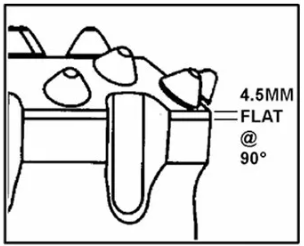
Grind the groove on the bevel. If necessary, grind the chamfered groove in a direction 4 degrees to the axial direction of the drill bit.
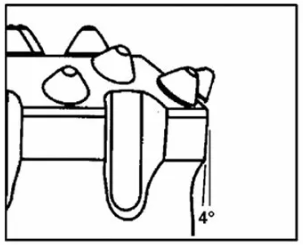
Make sure that the depth of the chip flute is appropriate, and regularly grind it to ensure that the drilled debris can be
discharged smoothly. Make sure that the chip flutes are not deformed, and if necessary, grind them.
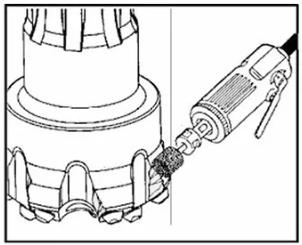
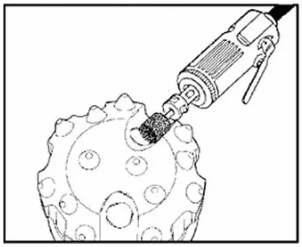